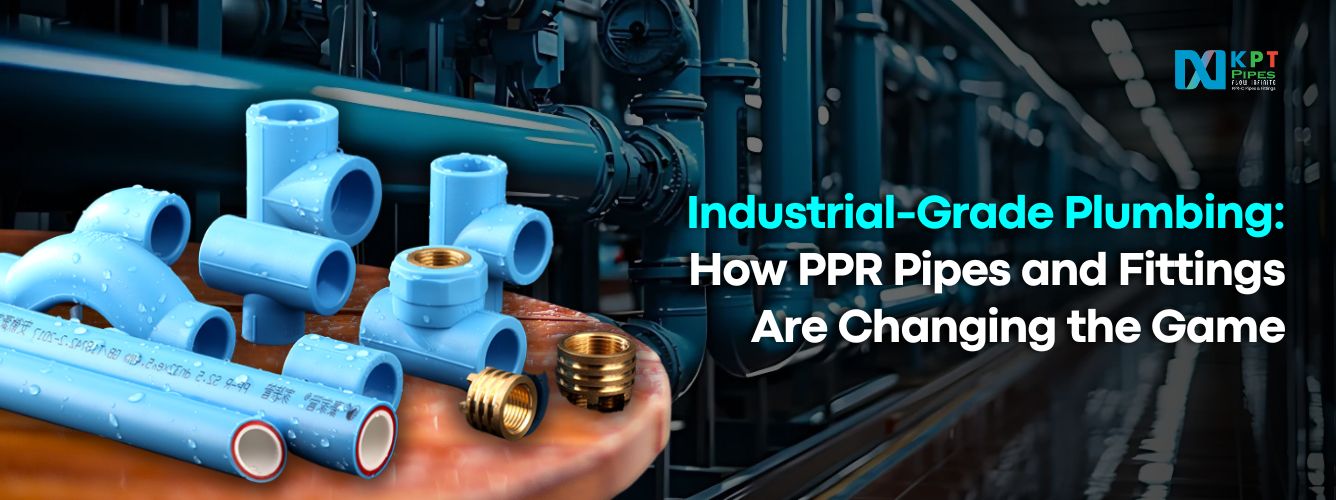
20 Mar Industrial-Grade Plumbing: How PPR Pipes and Fittings Are Changing the Game
In industrial settings, plumbing systems play a critical role in ensuring smooth operations. From transporting chemicals to managing high-pressure water systems, industrial-grade plumbing must be durable, reliable, and resistant to extreme conditions. Polypropylene Random Copolymer (PPR) pipes and fittings have emerged as the go-to solution for industrial plumbing due to their advanced properties. Unlike traditional materials like metal or PVC, PPR pipes and fittings offer high-temperature resistance, corrosion resistance, and longevity, making them a game-changer in industrial plumbing applications.
The Rise of PPR Pipes in Industrial Plumbing
PPR pipes and fittings represent a groundbreaking innovation in industrial-grade plumbing, providing a reliable and efficient solution for a wide variety of applications. Engineered to endure the harshest conditions, these pipes ensure that industrial systems continue to operate at peak performance for extended periods. The strength and adaptability of PPR pipes make them an ideal choice for industries requiring high-performance plumbing solutions, such as manufacturing, chemical processing, oil and gas, and water treatment. Their resistance to corrosion, chemicals, and extreme temperatures further enhances their appeal in demanding environments. The ability to maintain system integrity while reducing maintenance needs has cemented PPR pipes as a go-to option for industries looking for long-term cost savings and reliability. With their growing popularity, PPR pipes are reshaping the future of industrial plumbing.
The Growing Demand for PPR Industrial Pipes and Fittings
Industries such as manufacturing, chemical processing, pharmaceuticals, and food production require reliable industrial pipes that can withstand extreme conditions. Traditional materials like copper, galvanised steel, and PVC have been widely used, but they often face challenges such as corrosion, leakage, and high maintenance costs. Industrial pipes and fittings made from PPR have emerged as a game-changing solution that overcomes these issues while offering long-term benefits.
Why Industrial Plumbing Requires Advanced Solutions
Industrial plumbing systems deal with extreme pressures, harsh chemicals, and high temperatures. The materials used in these systems must withstand these conditions while ensuring efficiency, longevity, and cost-effectiveness. Traditional industrial pipes such as metal and PVC have limitations, such as corrosion, scaling, and high maintenance costs. PPR pipes and fittings, on the other hand, provide an innovative solution that meets industrial demands effectively.
Common Challenges in Industrial Plumbing:
- Corrosion and Scaling: Metal pipes corrode over time, leading to leaks and contamination.
- Temperature Sensitivity: Many plastic pipes cannot handle extreme temperatures.
- Chemical Resistance: Exposure to industrial chemicals can weaken traditional piping materials.
- Leakage Issues: Weak joints in conventional fittings lead to frequent leaks.
- High Maintenance Costs: Frequent repairs and replacements increase operational costs.
To address these challenges, industries are increasingly opting for PPR industrial pipes and fittings.
Why PPR Pipes Are Replacing Traditional Industrial Pipes:
PPR pipes are becoming the preferred choice over traditional industrial pipes like metal and PVC due to a range of significant advantages. These benefits make PPR pipe ideal for industries looking to improve efficiency, sustainability, and long-term cost savings.
Longevity and Durability
PPR pipes offer exceptional longevity, with a lifespan of over 50 years, even under extreme conditions. Unlike metal and PVC pipes that are prone to corrosion, scaling, and frequent replacements, PPR pipes remain durable and intact for decades. They are rust-proof and resistant to degradation from exposure to water, chemicals, and harsh environments, making them a superior choice for industries that rely on long-lasting infrastructure.
High-Temperature and Pressure Resistance
Industrial systems often deal with high temperatures and pressure, and PPR pipes excel in these conditions. They can withstand temperatures up to 95°C and pressures up to 20 bars, making them highly effective for transporting hot fluids in industries like manufacturing, chemical processing, and oil and gas. Their ability to maintain performance under extreme conditions further enhances their appeal in demanding industrial settings.
Corrosion and Chemical Resistance
One of the primary reasons for replacing traditional pipes with PPR is the material’s resistance to corrosion and chemicals. Metal pipes, which corrode over time, are not ideal for industries exposed to moisture and harsh chemicals. PPR pipes, on the other hand, are highly resistant to acids, alkalis, and industrial chemicals, ensuring reliability in applications such as water treatment, chemical processing, and oil and gas industries.
Leak-Proof System and Easy Installation
PPR pipes are designed with heat fusion technology that creates seamless, leak-proof joints. This eliminates the need for adhesives or welding agents, which are prone to failure and leakage in traditional piping systems. The fusion welding process ensures 100% sealed connections, reducing the risk of fluid loss and system failures. Moreover, the lightweight nature of PPR pipes makes them easy to transport and install, reducing both labor and transportation costs.
Cost-Effective Solution
While the initial cost of PPR pipes may be slightly higher than traditional options, their long lifespan, low maintenance, and energy efficiency result in significant cost savings over time. Their durability reduces the need for frequent replacements, and their ability to minimize heat loss in industrial systems helps lower energy consumption, making them an overall cost-effective choice for industrial applications.
Eco-Friendly and Sustainable
Industries are increasingly moving toward sustainable solutions, and PPR pipes align with green initiatives. These pipes are non-toxic and recyclable, making them an eco-friendly alternative to traditional materials. Their low carbon footprint and resistance to degradation contribute to a cleaner, more sustainable industrial operation.
Energy Efficiency and Thermal Insulation
In addition to their physical durability, PPR pipes provide excellent thermal insulation. This reduces heat loss in industrial heating systems, leading to lower energy consumption and improved system efficiency. By minimizing energy waste, PPR pipes help industries reduce their operational costs and environmental impact.
Key Industrial Applications of PPR Pipes and Fittings
PPR pipes and fittings are widely used across various industries due to their adaptability and resilience. Here are some key industrial applications:
Chemical and Pharmaceutical Industries
- Ideal for transporting chemicals and industrial solvents.
- Non-reactive nature ensures the purity of transported substances.
- High resistance to corrosion and scaling.
Food and Beverage Industry
- Ensures hygiene and safety for liquid food transport.
- Non-toxic and free from contaminants.
- Resistant to bacterial growth.
HVAC Systems in Industrial Buildings
- Used in industrial heating and cooling systems.
- Energy-efficient thermal insulation reduces operational costs.
Water Treatment and Plumbing Systems
- Used in industrial water filtration and distribution systems.
- Resistant to aggressive chemicals used in water treatment.
- Long lifespan ensures low maintenance requirements.
Oil and Gas Industry
- Reliable solution for transporting hot and pressurized fluids.
- High resistance to temperature fluctuations and chemical exposure.
Agricultural Irrigation Systems
- Ideal for high-pressure irrigation networks.
- Ensures efficient water distribution without contamination.
Conclusion
The demand for reliable, durable, and cost-effective industrial plumbing solutions has made PPR pipes and fittings the preferred choice for industries worldwide. Their high resistance to temperature, pressure, and chemicals, along with leak-proof joints and energy efficiency, makes them a superior alternative to traditional industrial pipes.
By investing in PPR industrial pipes and fittings, industries can reduce maintenance costs, improve efficiency, and ensure long-term reliability. As industrial plumbing continues to evolve, PPR pipes are set to revolutionize the way industries manage their plumbing systems.
FAQs (Frequently Asked Questions)
Q1. What makes PPR pipes suitable for industrial applications?
Ans: PPR pipes are highly durable, resistant to high temperatures and chemicals, and have leak-proof fusion-welded joints, making them ideal for industrial use.
Q2. How long do PPR pipes last in industrial settings?
Ans: PPR pipes have a lifespan of over 50 years, even under extreme industrial conditions.
Q3. Are PPR pipes better than metal pipes for industrial plumbing?
Ans: Yes, PPR pipes are corrosion-resistant, lightweight, and offer better thermal insulation, making them superior to traditional metal pipes.
Q4. Can PPR pipes handle high-pressure applications?
Ans: Yes, PPR pipes can withstand high pressures, making them suitable for industrial systems that require strong, reliable piping solutions.
Q5. Are PPR pipes environmentally friendly?
Ans: Yes, PPR pipes are non-toxic, recyclable, and eco-friendly, reducing environmental impact compared to other materials.