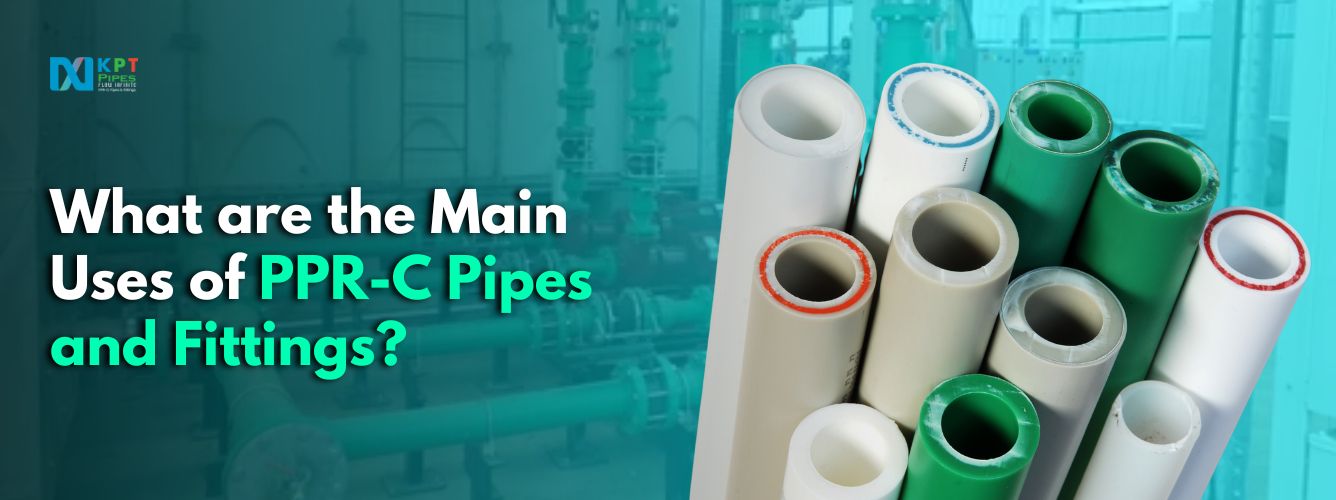
19 Dec What are the Main Uses of PPR-C Pipes and Fittings?
In the realm of modern plumbing and piping solutions, PPR-C pipes and fittings have emerged as an industry standard due to their exceptional properties. PPR-C, or Polypropylene Random Copolymer, is a type of plastic pipe known for its durability, resistance to high temperatures, and cost-effectiveness. This comprehensive guide will delve into the main uses of PPR-C pipes and fittings, highlighting why they have become the go-to choice for both residential and industrial applications.
What is PPR-C and Why Is It Popular?
PPR-C pipes are made from a copolymer of polypropylene and are often used in plumbing, irrigation, and other fluid transfer systems. The ‘C’ in PPR-C refers to copolymer, distinguishing it from other variations such as PPR-H (homopolymer). This specific type of polypropylene is modified to offer improved flexibility and strength, making it suitable for various applications.
PPR-C pipes are particularly popular due to their:
- High resistance to heat and pressure: PPR-C pipes are designed to withstand high temperatures, often up to 95°C (203°F), making them ideal for hot water systems. Their robust nature ensures reliable performance in demanding plumbing applications.
- Corrosion resistance: Unlike metal pipes that are prone to rust and corrosion, PPRC pipes remain unaffected by water and chemicals, ensuring long-term durability. This corrosion resistance eliminates maintenance issues commonly found with other materials.
- Low thermal conductivity: PPR-C pipes have low thermal conductivity, which helps to minimize heat loss in hot water systems. This energy-efficient feature contributes to reduced heating costs and greater overall system efficiency.
- Eco-friendliness: Made from 100% recyclable materials, PPR-C pipes offer a sustainable choice for plumbing systems. They reduce environmental impact by being reusable and minimizing waste during production and use.
- Ease of installation: PPR-C pipes utilize fusion welding techniques to create seamless, leak-proof joints. This method makes installation quick and efficient, reducing the potential for future leaks or maintenance problems.
Residential Applications of PPR-C Pipes and Fittings
Hot and Cold Water Supply Systems
One of the most common uses of PPR-C pipes is in residential water supply systems. Their durability and high-temperature resistance make them ideal for both hot and cold water plumbing. Whether it’s a new home construction or a renovation project, PPR-C pipes ensure a reliable, long-lasting plumbing system that doesn’t compromise on safety or performance.
Drinking Water Supply
PPR-C is non-toxic and doesn’t leach chemicals, which makes it suitable for potable water systems. The smooth interior surface of PPR-C pipes minimizes bacterial growth, ensuring that the water remains clean and safe for consumption.
Underfloor Heating Systems
Due to their excellent heat resistance and flexibility, PPRC pipes are commonly used in underfloor heating systems. They can handle the high temperatures associated with radiant floor heating without deformation, which helps in maintaining efficient heat distribution throughout the home.
Irrigation Systems
The robustness of PPR-C pipes makes them an excellent choice for irrigation networks. Whether used for garden watering, landscape irrigation, or agricultural systems, PPRC pipes can endure the pressure and weather conditions typical in outdoor settings.
Commercial and Industrial Uses of PPR-C Pipes and Fittings
Industrial Fluid Transfer
PPR-C pipes are widely used in industries for transporting various fluids, including hot and cold water, chemicals, and other non-corrosive liquids. Their resistance to chemical reactions and high temperatures ensures a safe and durable medium for transporting industrial fluids.
Compressed Air Systems
PPR-C fittings and pipes are also used in pneumatic systems to transport compressed air. Their strength and ability to handle high pressure without deforming or bursting make them suitable for both small-scale and large-scale applications in factories and manufacturing facilities.
Cooling Systems
Cooling systems, such as those found in HVAC (Heating, Ventilation, and Air Conditioning) setups, often incorporate PPR-C pipes for transporting coolants. The pipes’ resistance to both heat and pressure ensures that the cooling systems operate efficiently without any risk of leakage or failure.
Chemical Processing
Industries dealing with non-corrosive chemicals often use PPR-C pipes for their durability and resistance to chemical reactions. Their impermeable nature prevents the contamination of transported substances, making them ideal for use in pharmaceutical and food processing facilities.
Advantages of Using PPR-C Pipes and Fittings in Various Applications
Long Lifespan and Durability
PPRC pipes and fittings can last for decades without significant wear or failure. Their resistance to corrosion and degradation extends their service life, making them a cost-effective solution in both residential and industrial settings.
Easy Installation and Low Maintenance
The installation of PPR-C pipes is relatively straightforward, thanks to fusion welding that creates strong, leak-proof joints. This eliminates the need for complex fittings and minimizes potential weak points in the pipeline. Moreover, PPRC requires minimal maintenance, which further reduces long-term costs for homeowners and businesses.
Energy Efficiency
Due to their low thermal conductivity, PPR-C pipes are highly efficient in maintaining the temperature of the fluid they transport. This feature is particularly beneficial in water supply and heating systems, contributing to energy conservation and lower utility bills.
Safety and Hygiene
PPRC is resistant to bacterial and fungal growth, which is essential for maintaining the hygiene of water systems. Its smooth inner surface prevents sediment buildup, which can lead to clogging and contamination.
How PPR-C Pipes and Fittings Are Installed
Fusion Welding Process
The most common method of joining PPRC pipes is fusion welding, which creates a seamless and strong bond. The process involves heating the ends of the pipes and fittings until they melt and then pressing them together to form a solid connection. This technique ensures that the joints are leak-proof and can handle high-pressure and temperature conditions without failing.
Installation Tips:
- Cutting and Measuring: Use a proper pipe cutter to ensure clean, accurate cuts.
- Heating and Fusion: Use specialized fusion welding tools to achieve consistent heating.
- Alignment: Ensure the pipes and fittings are perfectly aligned before welding to prevent stress on the joints.
Types of Fittings Used with PPR-C Pipes
To complement PPR-C pipes, various fittings such as elbows, tees, couplings, and unions are available. These fittings are crucial for creating a comprehensive piping system that meets the specific needs of an installation. Uses of PPR-C include applications in hot and cold water systems, chemical transportation, and industrial fluid handling. PPR-C fittings are designed to be as durable and heat-resistant as the pipes themselves, ensuring uniformity throughout the plumbing or industrial system.
Specialty Fittings:
- Compression fittings for easy, temporary connections.
- Multi-directional fittings for complex layouts in industrial and commercial projects.
Conclusion
PPR-C pipes and fittings stand out in the world of plumbing and industrial systems for their unparalleled durability, temperature resistance, and versatility. The main uses of PPR-C include residential water supply, underfloor heating, irrigation systems, industrial fluid transfer, and more. With their easy installation, minimal maintenance requirements, and excellent performance, PPR-C pipes offer an ideal solution for anyone looking to invest in a reliable and efficient piping system.
When choosing a reliable supplier for your PPRC pipe needs, consider KPT Pipes. As a leading Pipes Manufacturing Company in India, KPT Pipes is committed to delivering high-quality PPR-C pipes and fittings that meet global standards and ensure lasting performance.
FAQs
Q1. What are the main benefits of using PPR-C pipes?
Ans: PPR-C pipes offer numerous advantages, including high resistance to heat and pressure, corrosion resistance, non-toxic properties, and low thermal conductivity. These features make them ideal for hot and cold water supply systems, underfloor heating, and industrial fluid transfer.
Q2. How long do PPR-C pipes last?
Ans: PPR-C pipes are known for their exceptional durability and can last for decades without significant wear or damage. Their lifespan is often around 50 years or more when properly installed and maintained, making them a cost-effective choice for both residential and industrial use.
Q3. What is the installation process for PPR-C pipes?
Ans: PPR-C pipes are typically installed using fusion welding, which involves heating the pipe ends until they melt and then joining them to create a seamless, leak-proof connection. This method ensures a strong, durable bond capable of handling high temperatures and pressures.